Digital print on wool fabrics - pretty lit!
- Susana Endesfelder
- Apr 5, 2024
- 2 min read

New technology has made way for digital printing on wool fabrics, revealing new design opportunities and markets for wool fabrications.
Benefits of digital printing

Digital fabric printing is where colour dyes are applied simultaneously in varying concentrations to a prepared fabric surface through inkjet technology, producing a printed fabric with intricate designs with infinite possibilities.
Traditionally used for synthetic fibres, leading innovators in the textile industry have now applied digital printing to wool fabric, opening up new applications for wool.

Digital printing
How the technology works ???
Digital fabric printing is a series of chemical processes whereby multiple water soluble colour dyes are applied simultaneously to a specially prepared fabric surface. Customised piezoelectric inkjet heads travelling back and forth across the fabric distributing the dye in varying concentrations, instructed by rasterised digital file embedded with colour management. This colour management works within the method of "controlled bleeding" to "chemical bonding" of dyes to the fabric.
THE PROCESS
STEP 1
FABRIC PREPARATION
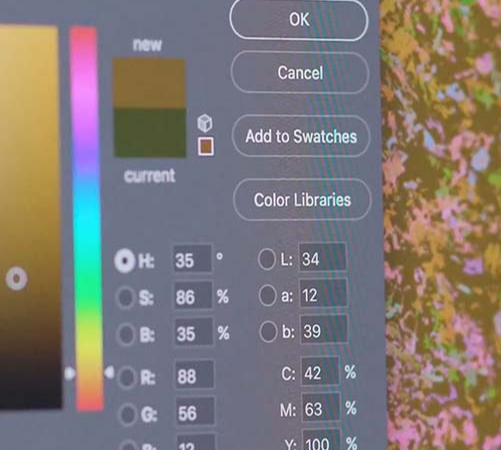
The ink used is a water soluble, modern textile dye. To stop the dyes from running and causing a blurring smudge, the fabric is first coated with a mixture of seaweed thickener, urea, salt and citric acid (lemon juice) to buffer the pH.
STEP 2
PRINTING

Tiny little random (stochastic) drops of dye, thinner than a hair, are sprinkled over the fabric from 8 different colour heads as the carriage passes across the fabric, which is held steady on the printer’s “sticky belt”. Eight base colours mixing together to produce over a billion colour combinations. 100% wool is dyed with acidic dyes or reactive dyes.
STEP 3
HEAT SETTING
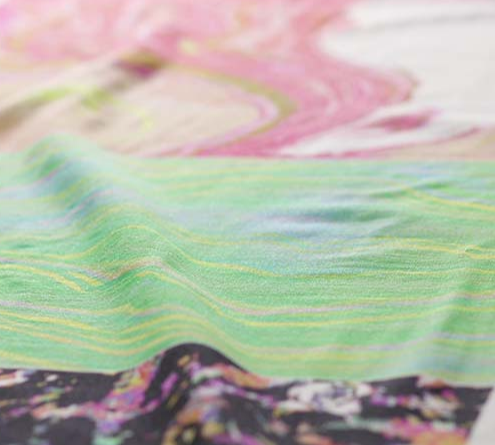
At first, the dye sits on the top of the fabric, which is then passed over a heat plate so that it is touch dry.
STEP 4
STEAMING
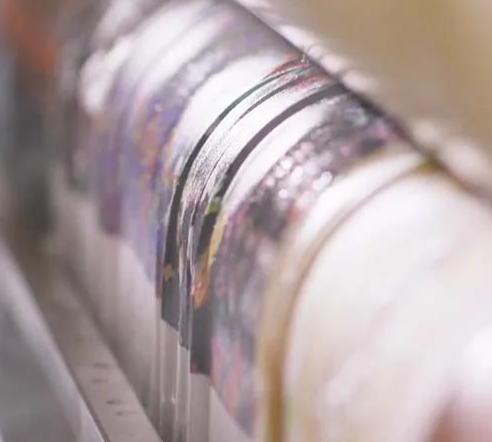
Steaming the fabric opens up the fibres and creates a waterway into and around the fibres so the dyes can travel from the surface of the fabric into the fibres, forming bonds and giving the fabric permanent colour, image and design.
STEP 5
RINSE COATING

Next, having done its job, the coating solution is washed out, along with the excess dyes (that did not bond), otherwise the colours would run in the rain. The result is a decorated fabric that retains its original feel and texture that can be made into garments, curtains, upholstery, scarves or, cushions – the possibility is endless.
My opinion on this:
You want to get into designing your own collection with no limits and use the recourse of sustainable fibres. This is the answer! Go for it!
Full color. Various design possibilities with full color and gradation print without the limitation of colors.
Quick delivery. Full color print is done in one process without using plates.
Color matching time is reduced.
Low cost.
Simple.
Small volume production.
High added value.
Environmentally friendly.
Source: @The Woolmark Company